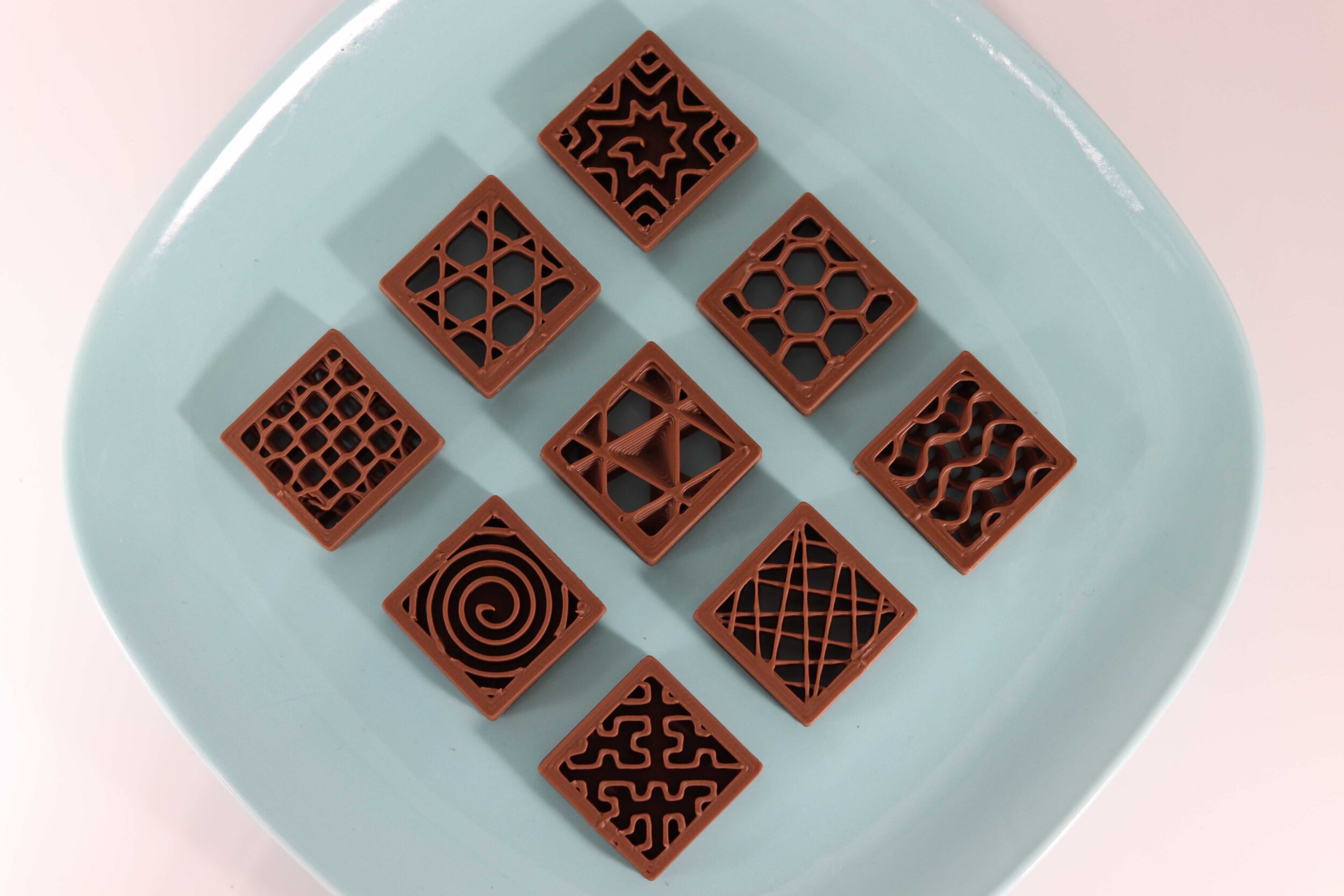
Cocoa Press:
Shaping the future of chocolate
Cocoa Press is a 3D printer that prints chocolate. It started in 2014 as an intro to engineering project during my senior year of high school. I continued working on Cocoa Press as my hobby throughout my time at the University of Pennsylvania, bringing it to trade shows and events. In 2018, my senior design team elected to work on Cocoa Press as our capstone project.
After graduating in 2019 with a degree in mechanical engineering, I turned my hobby into a business. Cocoa Press was selected for the Pennovation Accelerator and we set up shop in Philadelphia. Our business model included selling printers to chocolate shops, bakeries, and event planners as well as selling custom chocolates B2B and directly to consumers. Cocoa Press hopes to inspire confectionery innovation, enhance chocolate experiences, and spark creativity in everyone.
Check out our printer in action!
The many iterations of Cocoa Press
Version 1: 2014-2015
Cocoa Press started here. It had a custom plywood frame and motorized extruder but had no cooling abilities. I built it from the ground up with inspiration from a Makerbot Replicator I used to print most of the pieces.
Fun Fact: The tallest item this version printed was a 13 layer vase.
Version 1: Update 2017
This update used the same frame as the original. It utilized pneumatics for the extruder and peltiers to cool the chocolate after being extruded.
Fun Fact: This printer used custom circuitry in place of a stepper motor driver to open and close the pneumatic valve.
Version 2: ChocolaTier 2018-2019
ChocolaTier was my senior design capstone project at the University of Pennsylvania. It featured a sheet metal frame, pneumatic syringe and full vapor compression cooling system.
Fun Fact: ChocolaTier had 5 temperature sensors throughout the extruder for precision heating.
Version 3: Charlie 2019-2020
Charlie focused on ease of use, food safety, and design for manufacturing. It featured a stainless steel build chamber, new touch screen interface, and easily adjustable air pressure control. It used thermally conductive filament and 3D printed metal to quickly test hot end geometries.
Fun Fact: We had 4 trade shows lined up in the spring of 2020 to show Charlie off when COVID-19 hit the US.
Version 3: Update FrankenPrinter 2020
FrankenPrinter combined all of the best parts of our Charlie prototype with a brand new stepper motor driven extruder. This new extruder gave us much more accurate temperature and extrusion control and is the basis for our current design.
Fun Fact: FrankenPrinter switched from using single use plastic cartridges to a reusable stainless steel system.
Version 4: Chef 2020-Present
We tidied up every nut and bolt for Chef. It continues to utilize a vapor compression cooling system, an insulated build chamber, and a double-paned door. It has an updated, all-metal stepper motor driven extruder, and a frame made of food grade stainless steel and powder coated aluminum.
Fun Fact: Chef requires a custom thermistor circuit to have a chocolate temperature precision of +- 0.1°C.
As the Founder and CEO, I did a bit of everything
Business Models
With a new category of product, business models have not been defined yet. We had the opportunity to iterate and discover what worked and didn't work. The three main models we experimented with were selling hardware to hobbyists, selling hardware to businesses, and selling chocolate B2B and direct to consumer.
Intellectual Property
Even before Cocoa Press was my full time job, I knew my creation was new and unique. I filed a provisional patent in 2018 and a full utility patent in 2019. The patent application covers methods of precisely heating food products, extruding food products, sensing run out, and the use of a cooled enclosure.
Team
I hired and managed a team of four full-time employees. A dedicated and passionate team is the key to a successful business. It is also important to know when to outsource projects and when to complete them in-house. That is why we worked with multiple independent contractors and companies for work outside our skillset.
Here are some of the many technical challenges I overcame:
CAD
I designed Cocoa Press in SolidWorks. As the prototypes progressed, my CAD organization had to improve as well. For the latest version, I utilized master modeling to allow a single parameter in my primary sketch to adjust multiple parts at once. I designed parts for sheet metal, CNC milling, CNC lathe, and additive manufacturing.
Electrical
Of course, the printer wouldn’t run without its brain. I worked with a manufacturer to customize an existing 3D printer control board to increase the precision of temperature readings. I designed PCBs for signal filtering and for controlling a pneumatic valve, as well as a wire harness for faster printer assembly.
Supply Chain
An incredible design is only as valuable as your ability to make it. I coordinated with a dozen domestic and international suppliers to ensure components worked as expected. I worked through quality issues and shipping challenges to bring Cocoa Press to market.